Cables, Wire Harnesses and Connectors
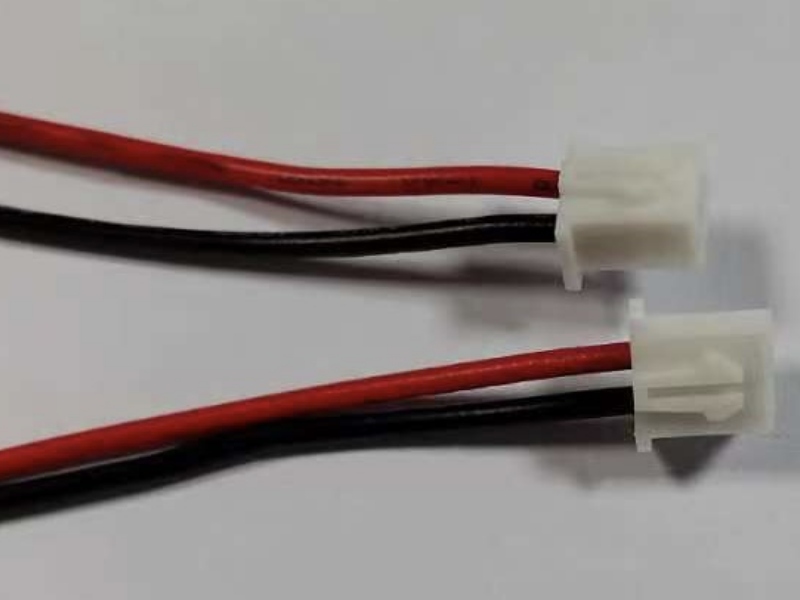
Custom Wire Solutions by E-BI
E-BI’s wire and cable formation team has over 20 years experience working with many different types of styles and materials. This experience allows for E-BI to help build any type of cables, wire harnesses, or connectors that a client might need. Our team is well versed in not only the design of these applications but in the production of them as well.
Cables and Wires
Here at E-BI we can help you not only manufacture your cable or wire, we can help with the design of it as well. The main difference between a wire and cable is that a wire a single conductor while a cable is two or more insulated wires wrapped in one jacket. Our team can help you determine what the right design and materials for your product are. Once we have determined these factors, using a five step process, we can help bring your idea to life.
Wire Drawing
This process consists of selecting the material to be used for wire/cable. The most common material types are copper or aluminum. This material is then prepared to be placed in the wire drawing machine. This machine pulls the wire through where it keeps the volume the same, the diameter decrease, and the length increases.
Annealing
During the drawing process, there needs to be tremendous pressure applied to the material to form a thinner wire. The finished wire must be flexible, this step allows for the wire to be softened, which is accomplished by heating the wire.
Stranding
In the case of manufacturing a cable, you will most likely need to strand the multiple wires together. These cables can be stranded together in a multitude of ways and are more flexible than just a solid wire. Stranding is an essential part of the cable manufacturing process.
Extrusion
Once the wires that need to have been stranded they are passed through an extruder. The same goes for the single wires. The extruder coats the wires and cables with a coating of plastic or another insulating material.
Cabling
Once the cable or wire has been prepared, the next and final step is to assemble the cable according to different utilities. For electrical and electronic cables that are used in everyday life, multiple strands of wires must be wrapped up interference-preventing layer if needed, into the protection jacket. In order to have a better forming degree, filler is often used to ensure the finished cable is round in shape. For cables that are more powerful and need to be buried underground, there are more protective measures:
- Bedding/inner sheath: This is usually a plastic layer that keeps the inner wires together and prepares it for steel armor.
- Steel armor: This is a steel layer that is made from the same material as the inner sheath. This prevents pests underground ruining the cable.
- Outer sheath: This is usually a layer that is made from the same material as the inner sheath. It is applied over the armor for protection against weather, chemicals, electrical, and mechanical components.
Wire Harness Connectors
Once we have helped you create your wire or cable, we can also help in the creation of the wire harness connector. Wire harnesses are bundles of electrical wires that each have their own individual covering but are also bound together using an additional outer covering. This harness keeps the electrical systems organized to transmit signals, relay information, or electrical power. They also protect the bound wires from constant friction, general wear, temperature extremes and other environmental conditions or potential damage that the harness may be exposed to. Manual assembly is still the most common method for wire harness manufacturing because routing cables or wires through sleeves is an extremely delicate process.