For contract manufacturing projects that aim to produce a product, project cost includes the overall works in design, engineering, manufacturing, quality, project management, and supply chain management. Within each of these categories, work can be divided into many sub-sectors with even more specialty tasks that intertwine with each other. Management teams try to put a budget on the project based on their best estimate. However, there are still many gray areas in the details of each task where decisions need to be made based on skills and best known methods (BKM). Without doing so, this is where the Snowflake Effect can be seen.
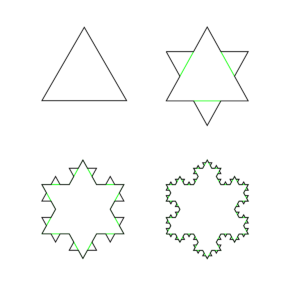
The Snowflake Effect relates to the work of Benoit Mandelbrot, a French and American mathematician, who was apioneer of fractal geometry. He noticed fractals occurring all over nature, such as with a snowflake, and in 1975 coined the term “fractal” to describe these irregular shapes that exhibited self-similar patterns at increasingly small scales. This helped answer the question of what is the total length of all sides of a snowflake. In short, it turns out the total length can be infinite. The result actually depends on how small of a measurement you use. The theory is that the smaller the measurement you use, the longer the total length. In other words, as a snowflake fractal evolves and more and more detail is revealed, the perimeter diverges to infinity, even though the total area remains a measurable finite amount. In applying this theory to project cost management, we discover that the cost of a project can be unlimited too. It all depends on how many details one wants to drill out during the operation.
Here are some examples:
At the design stage, one factor is determining the right cost for a new product in order to maximize sales. To make this decision, there is a cluster of second order questions such as what are the product’s quality requirements, size, style, touch and feel, functions, consumer segments, marketing cost, and so on. After many meetings and a lot of research, there might be a third order of questions—how do you prove or disprove the results of the second order questions? Then, a fourth order of questions ask how to verify the methodologies used on executing those works…This is where a perfect Snowflake Effect is formed. All of these layers of detail have great logical reasoning behind them. However, there is almost no way to stop this type of endless work without a decision maker stepping in at some stage.
Another example is the cost analysis of a product. As simple as it sounds, the first order of a product cost analysis spreadsheet usually consists of BOM cost for a certain volume, manufacturing cost, scraps, overhead, and profits. The second order of cost analysis will focus on each item on this spreadsheet, such as one piece part on the BOM list. This will lead to another round of cost analysis to a chip level. Then at chip level, there could be a third round of cost analysis to detail out seasons, distribution channels, tax structure, and even a fab cost analysis. This cost analysis process can keep going on making the workload grow exponentially. If no decision maker puts defined parameters in place at some point, the infinite factor of the Snowflake Effect occurs.
One last example is the root cause analysis of a product quality problem. When a problem appears on a product, in some cases the first order analysis involves looking into possible issues such as the people making the product, the equipment, materials, or methods. QA will collect data to prove or disprove each possible scenario as being the cause of the problem. Second order analysis would further detail each piece of the first order data. Similar questions can be asked such as who was managing the people, how were they trained, or what tool was being used. It could then go further with a third order that might ask questions to determine why things were done the way they were, what instruments were used, and so forth. This is the Snowflake Effect. As long as there is no budget, time, or resource limit, these works can keep on going.
Controlling the Snowflake Effect is a management principle. A decision maker has to step in at the right time and decide when to stop based on his or her assessment (skill and BKM) of the “area of a snowflake” or impact of the problem, versus the “length of all sides” or the amount of analytical work. When there is a lack of this control, people, or even an organization, can get lost in the process. Instead they tend to keep drilling into the details of an issue and forget about the bigger picture, which is the real impact each detail actually has on the project as a whole.
This principle applies to most management issues and even daily life. Missing the management balance between impact and amount of work can cause any small issue to grow to infinity in both time and cost, a type of “smart” failure.