Rapid Allocation of Backup Resources
By now many supply chain managers are sleepless, dealing with problems such as shipping delays, cost increases across the board, a shortage of materials, Covid-19 shutdowns, factories closing permanently, lingering trade wars, and the list goes on. The newest disruptions involve the shortage of energy such as electricity and natural gas. These affect all industries and even the average person’s daily life.
This is a time that is testing the resilience of global supply chains. At this level of challenge even Toyota, a pioneer of the Just-In-Time system, has had to shut down their production lines and delay the launch of new models.
Is there a way out of this mess?
Even though it may seem like there is no easy way out of these mammoth levels of disruptions, E-BI teams, as your manufacturing solution provider, are running full speed on all options and every tier of manufacturing to make things move more efficiently and effectively.
Manufacturing Resources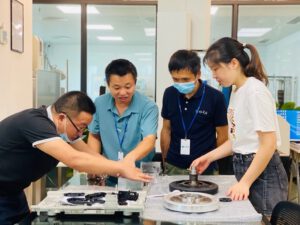
With our Star Factory Alliance of over 500 specialty partners, E-BI has been actively allocating capacity and materials among them to assure production and an on-time delivery 24 hours a day. E-BI specialists are working on getting problems solved in real-time, and activating back-up partners when needed to take over and make things happen. We have been minimizing the impacts of these disruptions, from material to shipping port selections, by avoiding the most congested ports.
Speed of Actions
Speed is the key for winning in a chaotic situation. When an opportunity calls for a Just-in-Time order, E-BI sourcing, logistics, and material purchasing teams have been working with clients on quick decisions such as spot purchasing of materials, bidding on shipping containers, and using less congested shipping ports. Day to day, E-BI project, engineering, and quality teams have been pushing through productions like playing a game of Chinese checkers, working through the night to adapt for power availability.
In reviewing the nature of all of the current disruptions, most of them have been a result of poor operational planning. For example, shipping cost increases are mostly because of freight forwarding companies not purchasing enough capacity from the ship lines, fearing less demand from the pandemic impact. When there was a sudden 6% increase in demand, this led to spot buying of spaces on ships, resulting in prices going through the roof. Similarly, the chip shortage was largely caused by lack of product production commitment. As a result, chip manufacturers shutdown lines and converted to new fabs. All these short term, temporary decisions add up to chaotic disruptions. As manufacturing and logistics companies acknowledge the faults in their operational planning, manufacturers will start reallocating production capacity to meet demands while logistics companies optimize space and routes. This will hopefully result in all of the problems going away in the next few months.